SOLUTIONS ET MATERIAUX. Afin de rendre le verre plat plus résistant aux rayures et lui conférer une plus longue durée de vie, un industriel a mis au point un procédé issu des technologies spatiales russes, baptisé "Diamondguard". Explications.
"Rendre le verre plus résistant aux rayures et plus durable, tel était le défi de notre R&D", explique Nicolas Gouzou, le directeur marketing France-Benelux de Guardian Industries, un des quatre grands acteurs mondiaux du verre plat. "A l'aide de notre technologie brevetée d'application sur le verre d'un revêtement au carbone, notre verre s'endommage moins en usage quotidien", poursuit-il. Plus résistant à l'abrasion et à l'usure, le verre protégé par le procédé Diamondguard présente un coefficient de friction très faible.
Pulvérisation d'une nanocouche de carbone
La technologie utilisée repose sur la pulvérisation cathodique, elle-même issue de la propulsion spatiale. Il s'agit en fait d'une méthode de dépôt d'une couche de carbone nanoscopique à la surface du verre dans une enceinte sous vide. Grâce à un champ magnétique orienté, la brume d'atomes de carbone vient combler les irrégularités de la surface, y fusionnent et constituent un réseau structurellement proche de celui qu'ils forment dans les diamants, conférant alors une extrême résistance. Cette couche protectrice, qui ne fait perdre qu'une infime partie de sa transparence au verre, est applicable à de nombreux types de vitrages : il est par exemple possible de traiter la surface extérieure d'un verre feuilleté ou celle d'un verre trempé. Il est également possible de pulvériser la nano-couche de carbone sur des miroirs, afin de les préserver des rayures, pour les cabines d'ascenseur notamment.
Multiples applications
L'industriel énumère de nombreuses applications possibles de ce verre plus endurant : surfaces murales, cloisons, rampes d'escaliers roulants, cabines d'ascenseur, présentoirs, comptoirs, tables de réunion ou de cuisine, portes de dressing… Des surfaces régulièrement soumises à des chocs avec des sacs à main, des montres ou bijoux, des stylos, des clés, des verres ou des tasses - ces dernières étant particulièrement agressives. Seules limites du traitement : il ne convient pas pour les sols, les rendant trop glissants, et il n'est pas adapté à une utilisation en extérieur, étant sensible aux UV. Produit haut de gamme, le verre traité conserve son aspect neuf plus longtemps qu'un vitrage ordinaire. Une aubaine pour certains hôtels, casinos et autres lieux touristiques à très forte affluence où le nombre de remplacements de portes vitrées est divisé par cinq ou six. "Diamondguard libère la créativité des architectes et des fabricants de meubles en leur permettant d'envisager le verre dans des applications où ils n'osaient que rarement l'utiliser. Pour les revendeurs de verre, il représente de nouvelles opportunités commerciales", explique Rolf Petrimichl, ingénieur R&D de Guardian. Reste une inconnue : le prix commercial de cette trouvaille technologique, dont le surcoût en production est déjà de l'ordre de 20 %. Le verre inrayable n'est pas encore tout à fait là, mais les ingénieurs s'en approchent…
Découvrez la fabrication du verre float et son traitement dans les pages suivantes.
Four
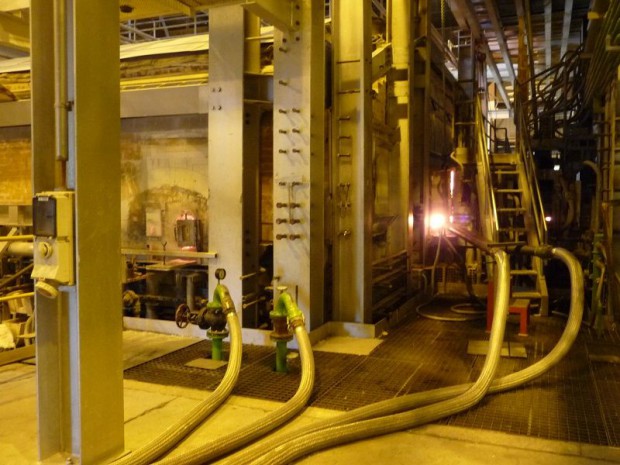
Dans un four en briques réfractaires, des brûleurs à gaz fonctionnant jour et nuit portent 670 tonnes de sable (et quelques additifs comme de la soude ou de la dolomie) à 1.600 °C afin de les faire fondre. L'équipement n'est jamais éteint et sa température doit être à la fois homogène et constante, afin d'assurer la qualité du verre obtenu.
Float
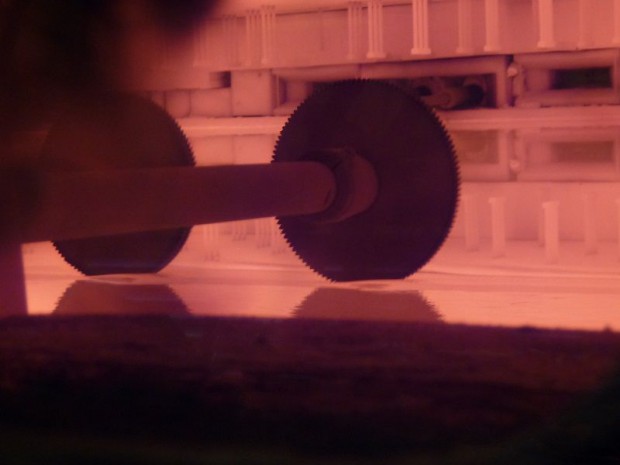
Le verre arrive du four par un canal et se répand sur un bain d'étain en fusion. La seule chaleur de la pate de verre à 1.100 °C suffit à maintenir le métal sous forme liquide. La densité plus faible du verre en fusion le maintient à la surface de l'étain, d'où le nom de "float". Les roues dentées ("top rollers") entraînent le verre encore liquide en s'accrochant sur les extrémités du ruban.
Centre de contrôle
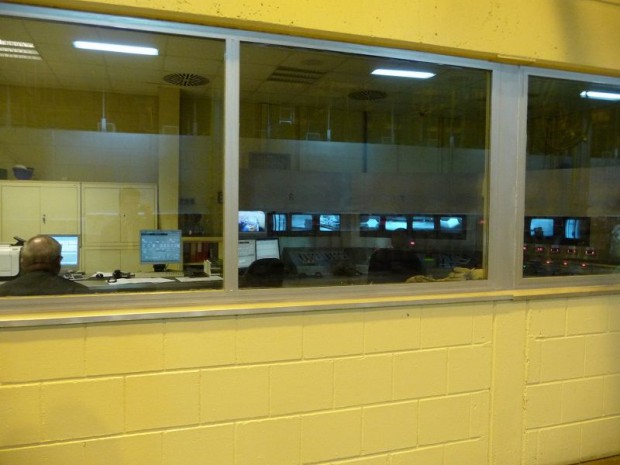
Des opérateurs se relaient jour et nuit afin de contrôler le processus. Ils le suivent sur des écrans où sont diffusées des images de caméras thermiques et des données de thermocouples.
Etenderie
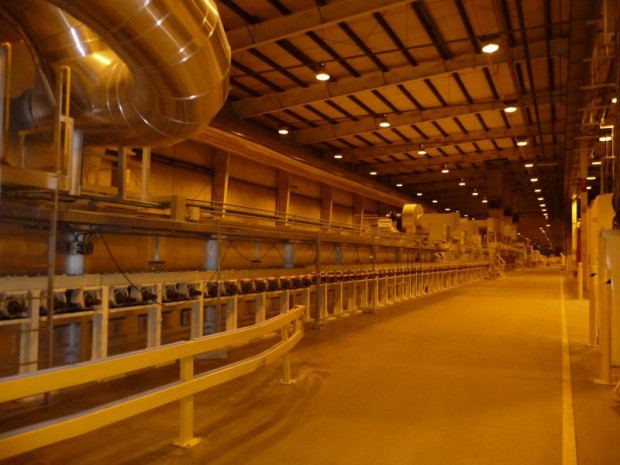
Le verre subit ensuite un processus de recuisson afin de contrôler les contraintes thermiques qui s'exercent en son sein. Les températures sont étroitement contrôlées dans le sens longitudinal et transversal du ruban qui avance en permanence. L'usine, qui ne s'arrête jamais, mesure 350 mètres de long.
Ruban
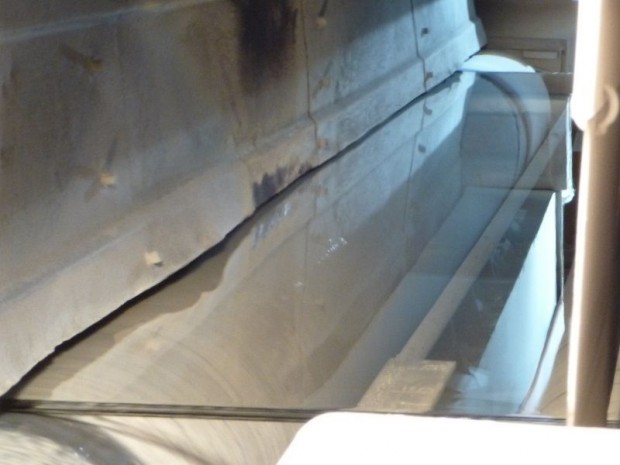
Le verre refroidi sort sous forme de ruban encore tiède. Des convoyeurs à rouleaux assurent alors son entraînement.
Rouleaux
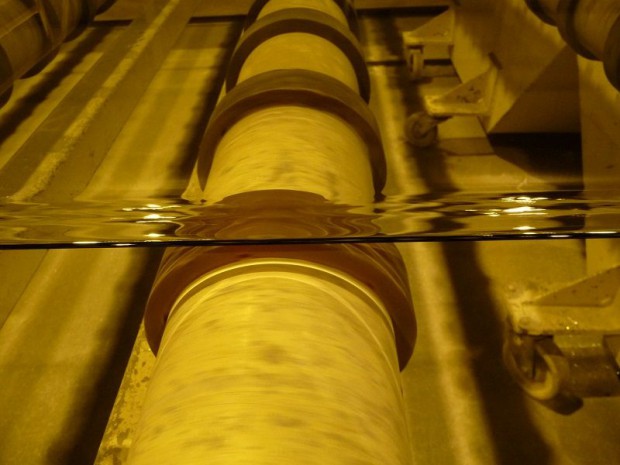
Seul les rebords du ruban de plus de 6 mètres de largeur et de quelques millimètres d'épaisseur (5 ou 6 mm en moyenne, variable en fonction de l'écartement et de la vitesse des top rollers) ne sont pas parfaitement lisses. Ils seront éliminés plus tard lors du processus de découpe.
Plaque
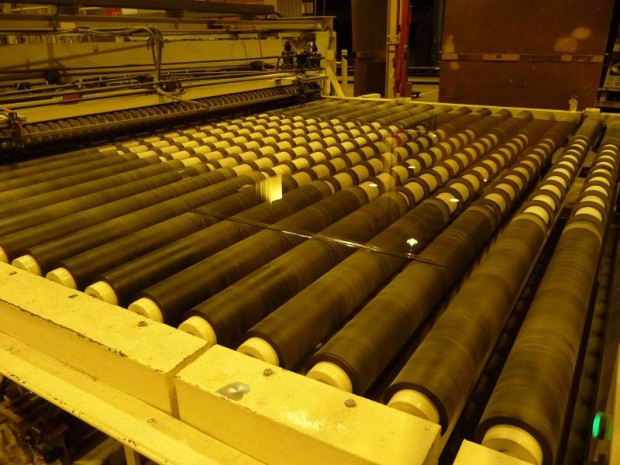
Le verre est découpé par des bras robotisés à une dimension standard de 6 x 3,21 mètres pour une utilisation dans le bâtiment ("Jumbo") ou dans d'autres sous-dimensions ("DLF").
Chevalets
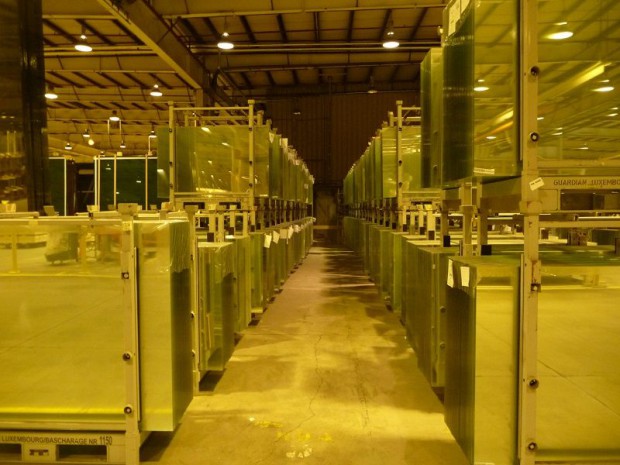
La production des plaques de verre aux différentes dimensions est ensuite stockée sur des chevalets avant un éventuel traitement ou l'expédition vers les utilisateurs (fenêtriers notamment).
Pertes
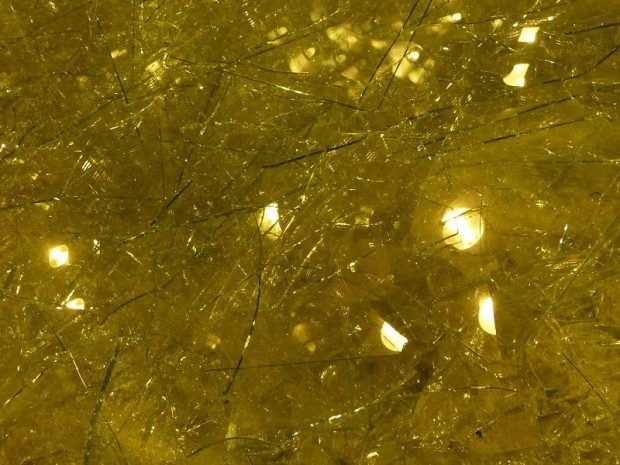
Les verres présentant un défaut sont éliminés. Mais ces chutes, ainsi que celles issues des découpes, forment le calcin, une matière première parfaitement recyclable. Rajoutée en amont, dans le four, elle permettra d'abaisser le point de fusion et d'économiser de l'énergie. Le taux de perte est d'environ 16 %.
Canons à ions
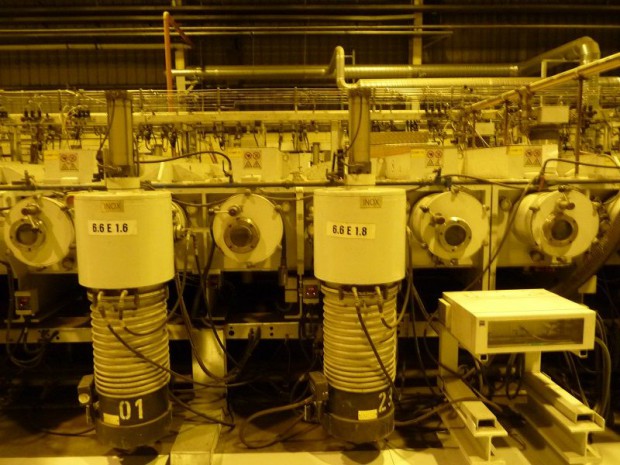
L'étape de traitement du verre intervient tout à la fin du processus. Les plaques de verre sont introduites dans une chambre sous vide et soumises à un champ magnétique. Une fine brume de carbone est ensuite pulvérisée sur une face de la plaque où les atomes se réorganisent et fusionnent afin de créer une couche résistante.