Située entre le Mans (72) et Laval (53), la carrière de Neau « Chaux et Dolomie Françaises » est l'unique site à extraire et fabriquer de la chaux aérienne dolomitique en France. Le groupe belge Lhoist, propriétaire des trois carrières à ciel ouvert gravitant autour de l'usine, nous a ouvert ses portes. L'occasion de découvrir les différentes étapes de traitement de la chaux, de l'extraction à la fabrication finale. Visite.
« Chaux et Dolomie Françaises » constituent en France le seul exemple de carrière de chaux aérienne dolomitique. Fondées en 1871 et rachetées par le groupe belge Lhoist en 1980, elles approvisionnent toute la région grâce à trois sites de gisement dolomitiques(Geslin, La Gare et Torcé)fonctionnant sept jours sur sept et dont l'exploitation a été autorisée par arrêté préfectoral pour plus de cinquante ans,soit une réserve de 30 millions de tonnes.
Exploitation et production quasi instantanées
A Neau, 350.000 tonnes de chaux sont produites annuellement. Les sites de La Gare et Geslin sont exploités directement, de la carrière à l'usine, toute proche. Pour Torcé, située plus loin, la pierre est préparée sur place par un sous-traitant puis acheminée en usine.
« Après avoir découvert les gisements, l'équipe procède au forage qui consiste à creuser par palier de 15 m de profondeur à chaque fois, le maximum autorisé, plusieurs paliers de 15 m seront réalisés. Le site de Geslin atteint ainsi à ce jour une profondeur de - 65 m », commente Philippe Merceleau, directeur de la Région nord-ouest, Balthazard et Cotte du groupe.
L'extraction des pierres est effectuée par tirs d'explosifs.Une fois les blocs séparés, ils sont concassés à l'aide de deux concasseurs à mâchoires qui tournent à plein régime toute l'année. Les premiers « morceaux » sont acheminés afin d'être lavés. Si besoin un concassage secondaire interviendra. L'eau ayant servi au lavage sera recyclée via un bassin de sédimentation.
Le broyage constitue la troisième étape de la production, « il se fait lorsque la pierre est crue. Une partie est directement proposée ainsi, avec un broyage de 80 microns, l'autre partie est acheminée vers des fours », précise Xavier Greco, directeur de l'usine. Pour Daniel Daviller, directeur général de BCB, le centre d'expertise bâtiment de Lhoist, la cuisson constitue une phase décisive pour la qualité du matériau : « Elle est réalisée à l'aide de deux fours droits verticaux identiques constitués de deux ou trois cuves reliées entre elles par un canal de liaison doublé d'une chemise de briques réfractaires. L'usine de Neau utilise également un four rotatif (avec grille de préchauffage) datant d'avant-guerre. Les trois fours sont alimentés en gaz coke de pétrole, une substance solide dérivée du pétrole et utilisée comme combustible ». D'autres sont usités sur les six autres usines que compte Lhoist en France : pépin de raisin, granulés de bois, etc, offrant ainsi des alternatives plus respectueuses de l'environnement.
La cuisson, ou carbonatation, à 1.000 C°, permet d'obtenir des morceaux de chaux. Ceux-ci seront calibrés en petits morceaux de 3 à 7 mm ou en poudre de 0 à 3 mm en repassant par une nouvelle étape de broyage. Enfin, le dernier stade consiste à hydrater la chaux dans un atelier d'hydratation afin d'obtenir une chaux éteinte qui sera criblée c'est-à-dire classifiée en fonction de ses propriétés (magnésienne, calcique…)et des besoins du client. Pour 500 kg de chaux, il faut 1 tonne de calcaire.
Un contrôle de qualité permanent
A Neau, la qualité chimique de la pierre est vérifiée continuellement, 7.000 échantillons sont ainsi analysés annuellement par deux personnes du laboratoire de l'usine. Chaux aérienne,chaux formulées, béton chanvre, Batidol (une chaux nouvelle génération)… l'unité à Neau dispose de 400 références produit. Certifiée ISO 9001, relative aux systèmes de gestion de la qualité, elle fait aujourd'hui l'objet d'un programme d'investissement de la part de Lhoist, 5 millions d'euros sont consacrés à la modernisation du process pour obtenir une qualité du produit optimum. Au total, l'unité de production est équipée de 47 silos, 12 broyeurs, 11 cribles. Deux établissements de stockage et trois dépôts complètent l'installation.
La chaux, un produit trop méconnu dans la construction
Principalement utilisée dans le secteur de l'agriculture, pour recouvrir les sols, et dans les travaux publics, la chaux aérienne dolomitique se révèle pourtant être d'une qualité extrêmement pure, sa teneur en magnésium dépasse les 30 %. Une pureté que Lhoist souhaite aujourd'hui mettre au service de la construction, un secteur qui ne représente actuellement que 7 % du marché. Daniel Daviller, mise sur la qualité : « La chaux, c'est le sel de l'industrie, on en trouve partout. Dans le bâtiment, 90 % des professionnels utilisent du mortier prêt à l'emploi, une option peu écologique. Nous avons fait le choix du mélange sur le chantier, seul le liant est transporté. Avec la chaux, on fait sa maison du maçonnage à la finition, on retombe sur des mises en œuvre historiques ». Conscient de la nécessité de « réapprendre » aux professionnels la mise en œuvre de la chaux, le groupe propose des formations tout au long de l'année.
La chaux dolomitique
Extraction raisonnée
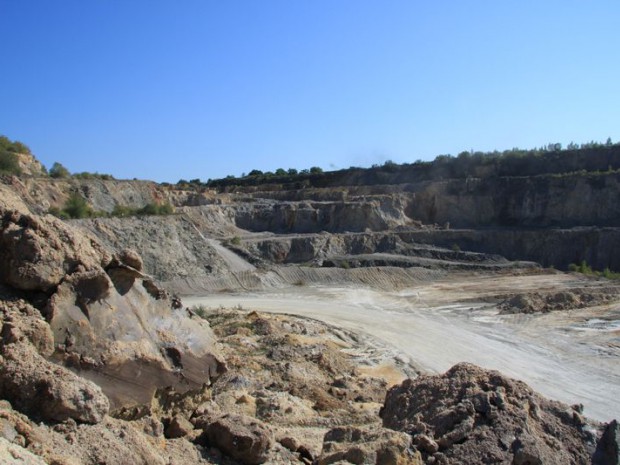
Cinquante ans
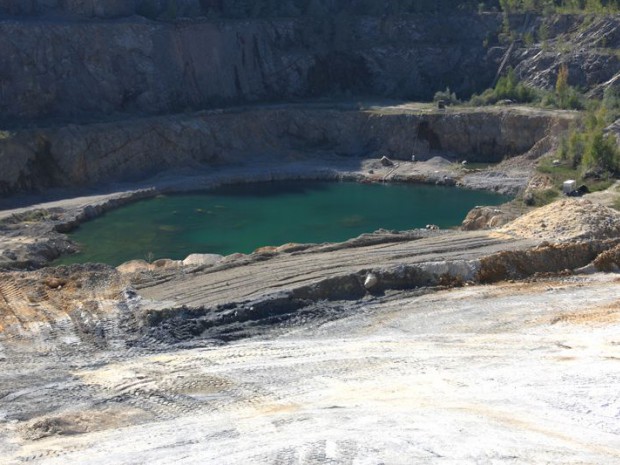
Un process plus performant

Des fours droits
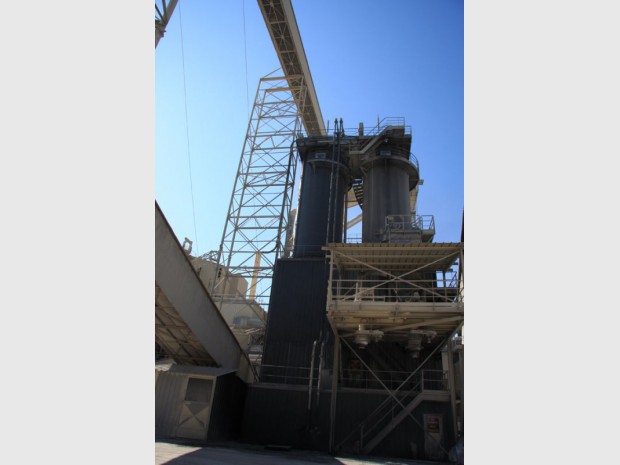
Un four d'avant-guerre
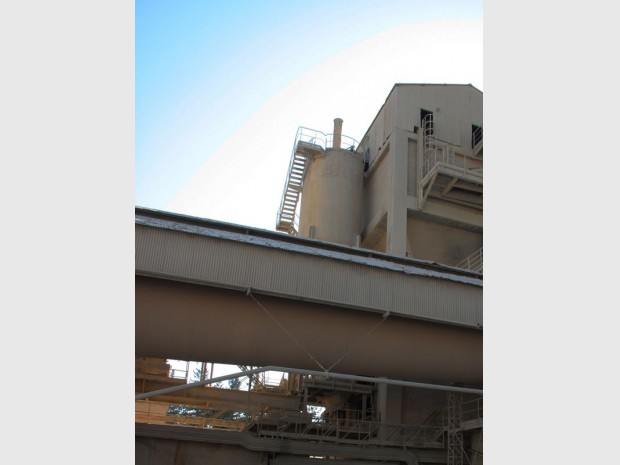
De la carrière à l'usine
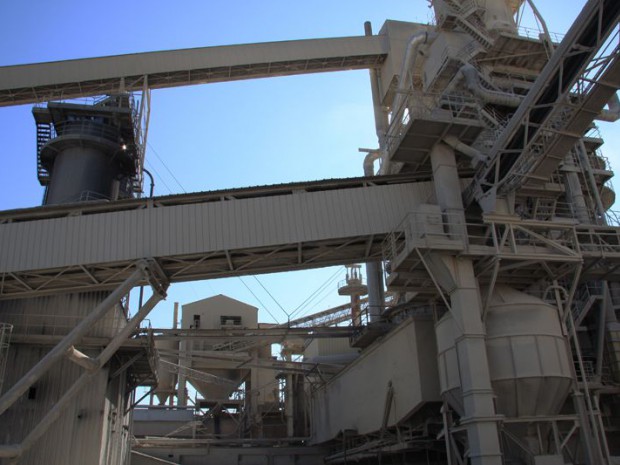
Une entreprise "familiale"
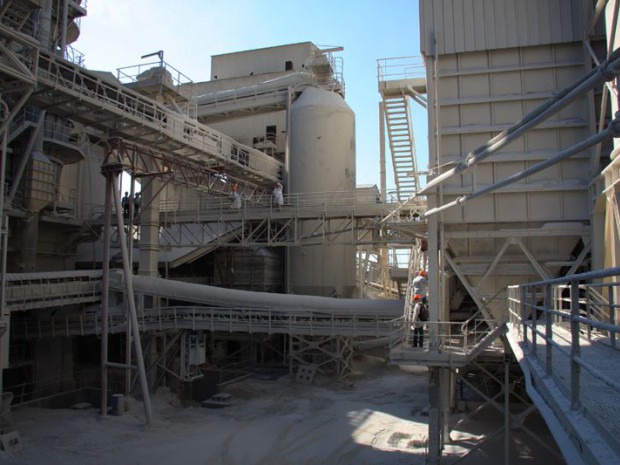
A plein régime
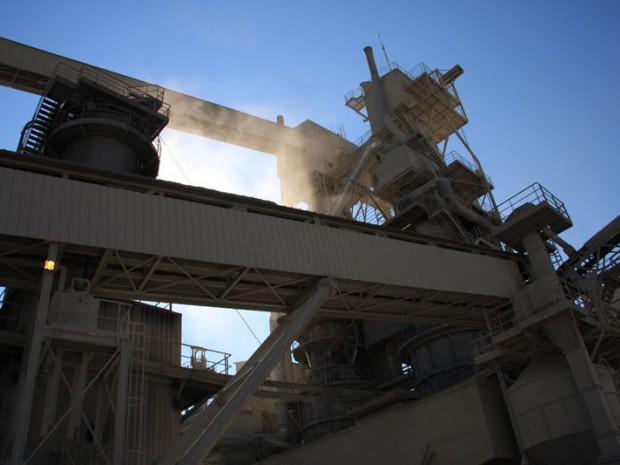
Une offre globale
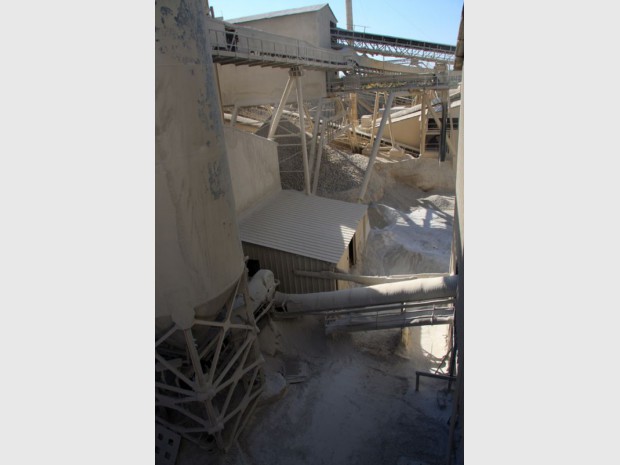
BCB, le centre d'expertise bâtiment du groupe Lhoist
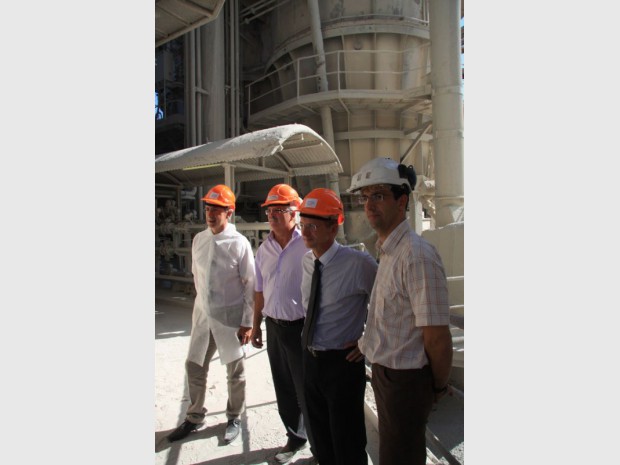
Philippe Merceleau, directeur de la Région Nord Ouest - Balthazard et Cotte - Groupe Lhoist; Daniel Daviller, directeur Général Délégué de BCB, Xavier Greco, directeur usine Chaux et Dolomie Françaises - Groupe Lhoist
Plusieurs fonctions
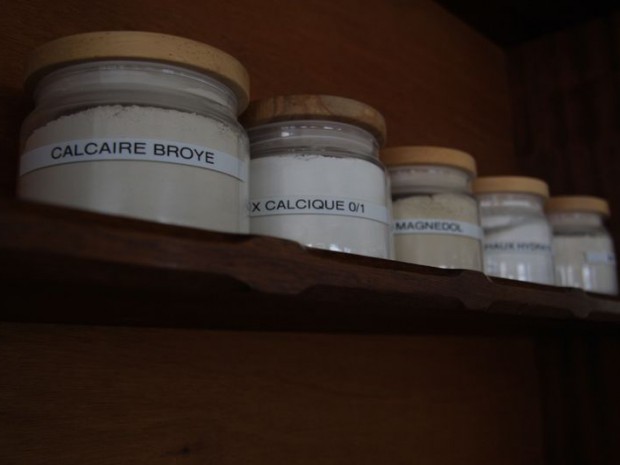
Des contrôles permanents
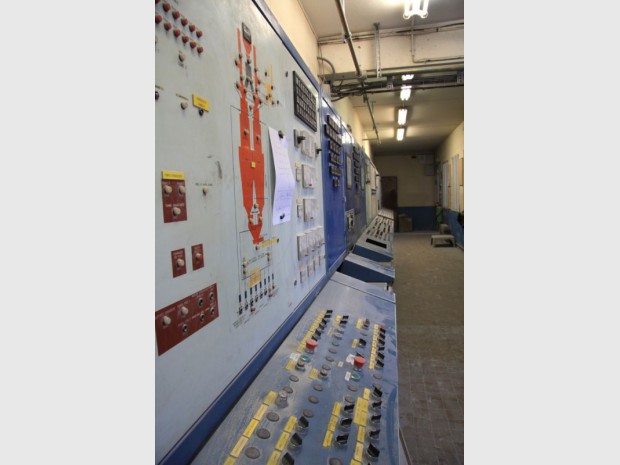
L'unité de production dispose de la certification ISO 9001, relative aux systèmes de gestion de la qualité.
Flux continu
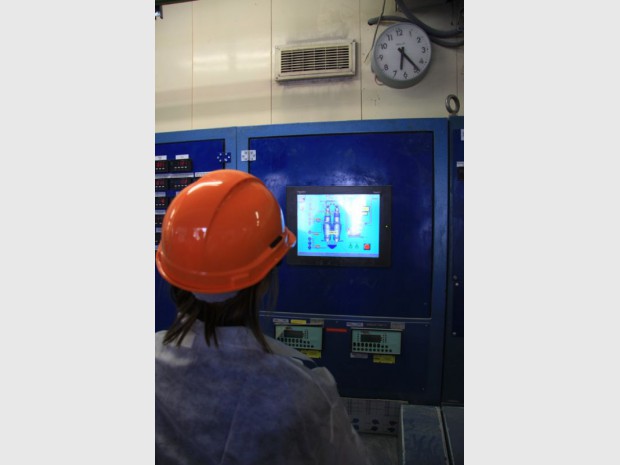
De la carrière à l'usine
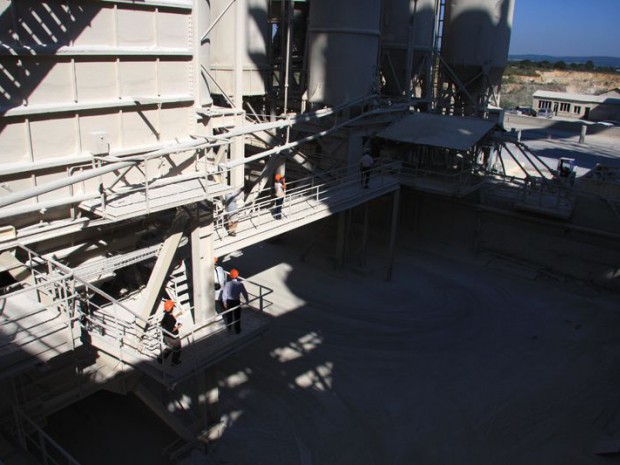
Qualité chimique de la pierre
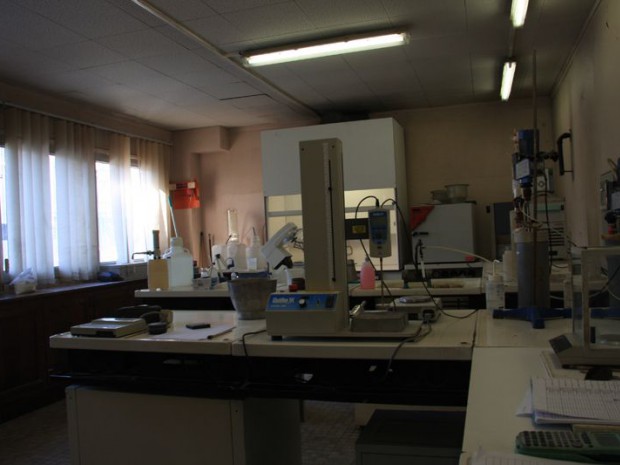
Trois carrières pour Neau
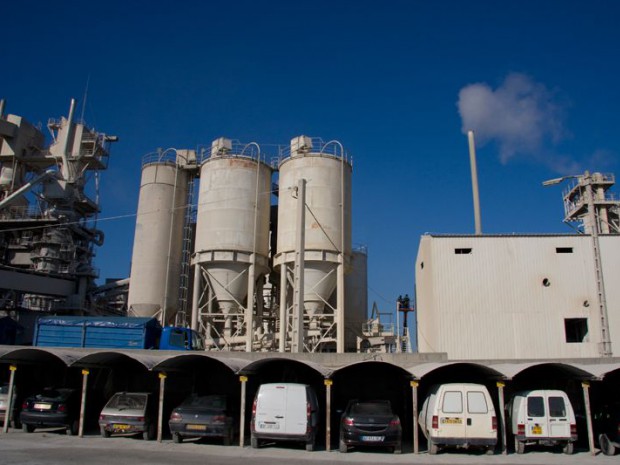
Défi à venir
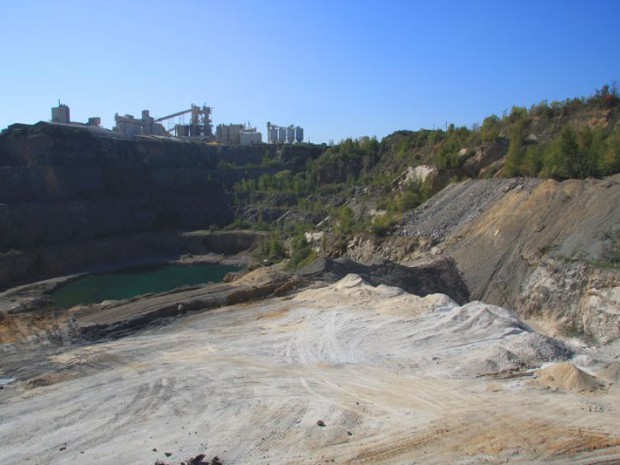
55.000 tonnes de chaux dolomitique / an
180.000 tonnes de chaux vive / an
2.500 tonnes de chaux magnésienne éteinte / an
32.000 tonnes de chaux calcique éteinte / an