Afin de répondre à la demande de plus en plus importante d'isolants durables comme la laine minérale, Knauf a récemment inauguré, au travers de sa filiale isolation, Knauf Insulation, une nouvelle usine, à Lannemezan (65). Couvrant plus de 200.000 m2 de surface, cette usine est dédiée à la fabrication de laines élaborées avec le procédé Ecose® Technology. Détails.
L'ouverture de la nouvelle usine Knauf Insulation, en mai dernier à Lannemezan dans les Hautes-Pyrénées et à seulement 50 kilomètres de la frontière espagnole, représente le nouveau standard de fabrication d'isolants de la marque. Cette nouvelle usine permet, en effet, de répondre à la demande croissante de la toute récente génération de laines minérales conçue avec le procédé Ecose® Technology, procédé déjà utilisé dans l'usine Knauf de Visé en Belgique, et développé par l'industriel allemand, spécialisé dans le bâtiment et l'isolation de maisons.
Bâti en lieu et place de l'ancienne usine d'aluminium Alcan, sur une surface de plus de 200.000 m² et pour un montant de 140 millions d'euros, le site de Lannemezan est composé de bâtiments affectés à la production représentant 28.524 m², d'une partie office et magasins de 8.760 m2, et d'une zone réservée au stockage des produits finis couvrant plus de 26.000 m², soit «l'équivalent de 5.000 tonnes de produits finis», souligne Philippe Nguyen, directeur du site. La direction de l'usine et les services administratifs occupent une surface de 2.500 m² de bureaux.
Ainsi, cette usine a été construite pour produire la laine minérale de verre élaborée avec Ecose® Technology et fabriquée à partir de matières premières naturellement renouvelables et/ou recyclées, utilisant un liant à base végétale, ne contenant pas de formaldéhyde, de phénol ou d'acrylique et sans adjonction de colorants artificiels ou de pigments. Cette laine, «sans odeur et générant moins de poussière est donc plus agréable à poser», souligne Jean-Jacques Pontailler, directeur général France, Knauf Insulation. «Et elle est tellement plus douce, qu'on pourrait se démaquiller avec», ironise ce dernier.
Avec ce procédé, Knauf Insulation marque de façon significative une étape majeure dans le cadre de sa politique industrielle de développement durable. En effet, «la fabrication de cette laine minérale permet d'économiser plus de 200 fois l'énergie utilisée à sa production», explique le directeur du site.
Knauf, conscient de l'environnement
Toujours conformément à sa politique de développement durable, l'entreprise, s'est dotée d'un four de fusion, de 72 mètres de long et de 14 mètres de large utilisant la technologie oxygaz associée à l'énergie électrique. Une partie de la toiture du site est équipée d'un ensemble de 8.760 m² de membranes photovoltaïques qui produit 420 MWh/an d'énergie électrique, «soit l'équivalent de la consommation annuelle d'environ 100 maisons individuelles chauffées à l'électricité», ajoute le directeur du site. L'usine est également équipée d'un double filtrage de l'air et d'un système d'eau en circuit fermé. Knauf Insulation a également augmenté la quantité de matières recyclées dans son process de production.
Enfin, pour une parfaite intégration du site dans son cadre environnemental, l'aspect esthétique de l'usine a largement été pris en compte. «Tout a été mis en œuvre pour minimiser l'impact visuel. L'usine intègre des espaces verts ainsi que plus de 300 variétés d'arbres», souligne Nadine Grard, directrice Marketing et Communication. «Situé au pied des Pyrénées, le site entraîne une réduction significative des coûts de transport, réduisant de ce fait leurs impacts environnementaux», conclut celle-ci.
Usine Knauf Insulation
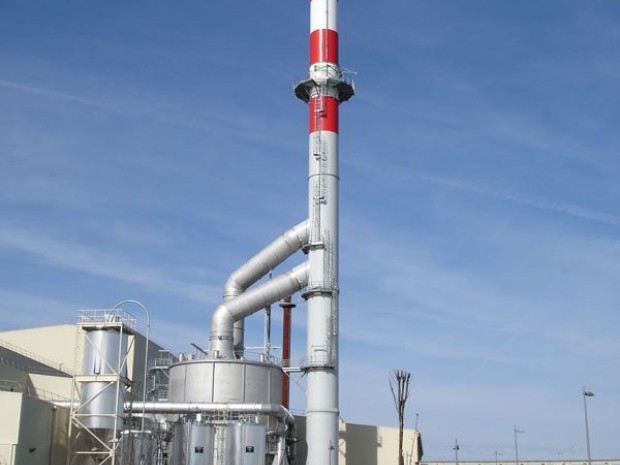
Opérationnelle depuis avril 2010, l'usine Knauf Insulation de Lanemezan (65)peut produire 70.000 tonnes de laines minérales.
Process de production
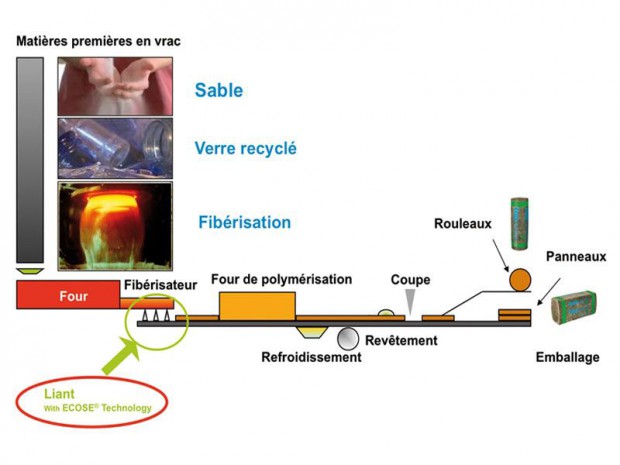
Le process de production de la laine minérale de verre.
Zone de stockage
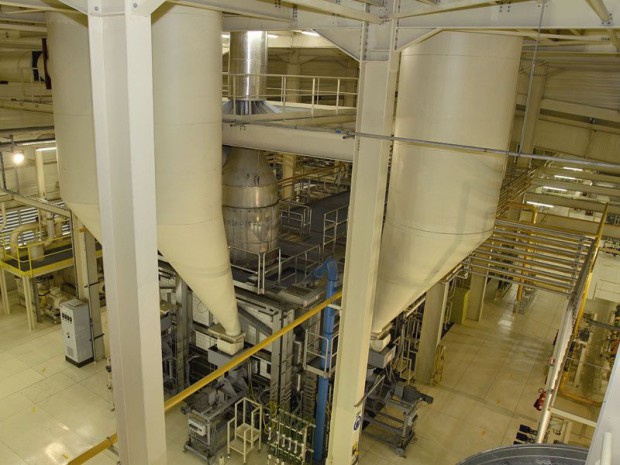
Toutes les matières premières sont strictement contrôlées à leur entrée. Que ce soit le verre interne qui a été recyclé de la fusion, le verre externe recyclé qui provient de bouteilles et pare-brise de véhicules hors d'usage, le sable, la dolomite, le carbonate de sodium et le borate de sodium.
Le four de fusion
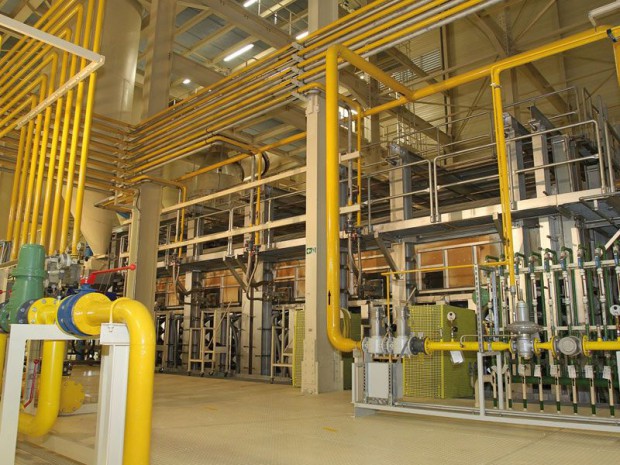
Ici, les matières premières sont introduites dans le four grâce à un système assisté par ordinateur. Le type de combustion est un mélange oxygène et gaz, boosté par l'énergie électrique. La température y est de 1.200 degrés.
Le four de polymérisation
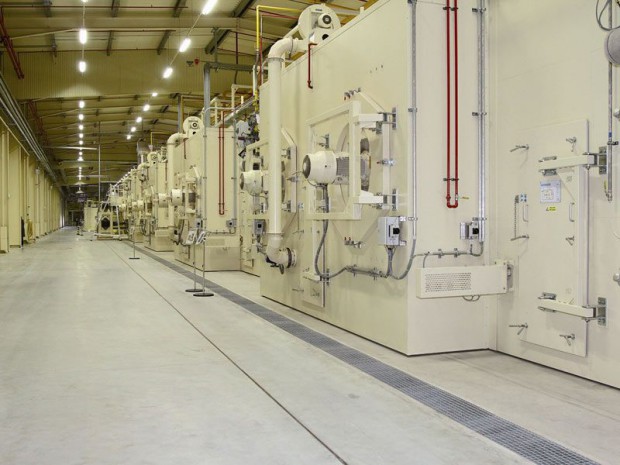
Après la fusion, vient la phase de la fibérisation, c'est lorsque la matière en fusion passe à travers des assiettes de fibérisation, qui sont percées d'une multitude d'ouvertures, et se transforme en fibres grâce à la force centrifuge. C'est à cet instant que le liant Ecose® Technology est ajouté aux fibres.
Puis s'ensuit le forming, où les fibres sont refroidies par pression d'air et acheminées sur une bande transporteuse. La largeur du matelas est de 2.400 mm.
Enfin, la phase de polymérisation avec son four, c'est l'action de la chaleur qui est d'environ 250 degrés sur le liant, et qui permet de lier les fibres entre elles. L'épaisseur finale du produit est ainsi définie.
La zone froide
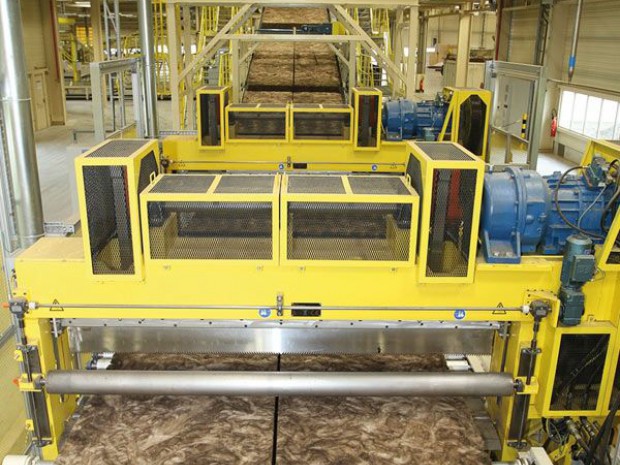
Après refroidissement, le matelas passe sur un poste de pose de revêtement (papier kraft, voile de verre, voile soft…), puis par des scies de rive pour des bords nets. Une guillotine coupe rouleaux et panneaux aux dimensions requises. Les lames de coupe peuvent produire jusqu'à 90 coups/min.
Mise en place des codes
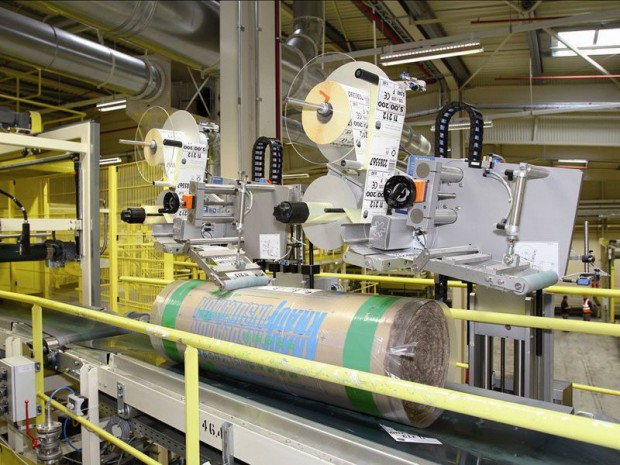
En amont, l'enrouleuse forme les rouleaux et les enveloppes d'un film transparent en polyéthylène. L'empileuse permet de faire des paquets de panneaux au rythme de 11 paquets par minute. Les rouleaux et les panneaux sont comprimés jusqu'à 7 fois pour minimiser leur volume de transport, et optimiser la gestion des stocks des clients.
Pour planchers
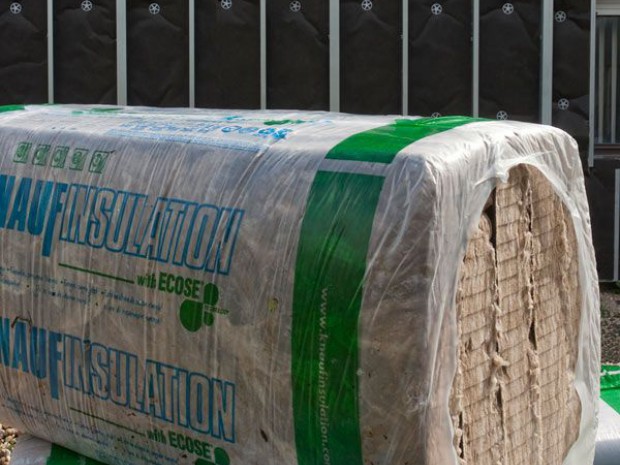
En dehors des rouleaux de laine, Knauf crée également des tablettes destinées plus particulièrement à la rénovation des planchers.
La zone de stockage d'une superficie de 26.000 m2
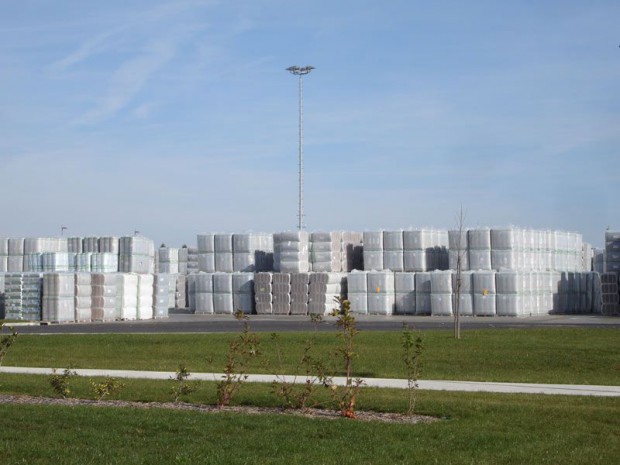
Ici, sur cette zone de stockage, l'équivalent de 5.000 tonnes de produits peuvent être entreposés.
Une situation stratégique pour Knauf Insulation
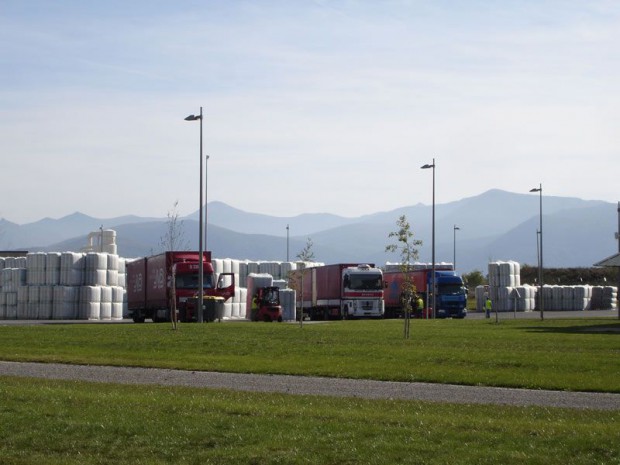
A une cinquantaine de kilomètres de la frontière espagnole le site entraîne une réduction significative des coûts de transport, réduisant de ce fait leurs impacts environnementaux.
Surface totale : plus de 200.000 m2 dont une option sur 85.668 m2
Début/fin des travaux : Nov 2007 / Début 2010
Démarrage du site : 24 avril 2010
1ère expédition : 01 juin 2010
Montant de l'investissement : 140 millions d'euros
Capacité actuelle de l'usine : 70.000 tonnes
Capacité additionnelle : 20.000 tonnes